Autonomous Mobile Robot (AMR) Repair
Diagnosing Issues in Autonomous Mobile Robots (AMRs)
Autonomous Mobile Robots (AMRs) are complex systems that require precise diagnostics to ensure they function properly. AMR repair involves identifying a range of potential issues such as navigation failures, battery malfunctions, or communication errors. Our experts are trained to troubleshoot and diagnose problems quickly, ensuring minimal downtime for your robots.
Common issues with AMRs include:
Battery failures and charging issues
Navigation errors due to environmental factors or sensor malfunctions
Software glitches or system compatibility problems
Motor malfunctions affecting movement and efficiency
We use advanced diagnostic tools to identify and resolve issues efficiently, keeping your autonomous mobile robots working at peak performance.

Our AMR Repair and Testing Procedures
When it comes to AMR repair, we follow a rigorous, step-by-step process to ensure your robots are fully operational after repairs. Our AMR repair services include both hardware and software checks, as well as extensive testing to verify system functionality. Our goal is to restore your mobile robots to optimal conditions, ensuring they can safely and efficiently navigate your environment.
Our repair procedure includes:
Diagnostic Testing: Identifying the root cause of failure or malfunction.
Component Replacement: Replacing faulty parts such as sensors, batteries, or motors.
Software Updates: Updating or troubleshooting the software to ensure smooth operation.
System Calibration: Calibrating the robot’s navigation and sensors to ensure accurate performance.
Post-Repair Testing: Running multiple tests to verify the functionality of the robot.
By providing thorough testing after repairs, we ensure that your autonomous mobile robots continue to meet your operational needs.
Maintenance Strategies for Mobile Robot Fleets
Regular AMR maintenance prevents breakdowns and extends the life of your robotic fleet. Our service programs are designed to meet your scheduling, uptime, and workflow needs—no matter the size of your AMR deployment.
We recommend monthly or quarterly maintenance depending on runtime hours, environment, and payloads. Services include wheel wear inspections, sensor calibration, brake testing, encoder cleaning, charging port checks, and firmware stability reviews.
For high-cycle facilities, our preventive maintenance keeps your mobile robots aligned, efficient, and ready to handle growing volume. And when a unit starts to drift or slow down, we catch it before it fails.


Common AMR Failures and How We Fix Them
Mobile robots face unique wear patterns and failure points based on their operating conditions. We’ve seen it all—from software misconfiguration to LiDAR blind spots—and we know how to fix it fast.
Some common problems include:
Unstable mapping or localization
Battery charging inconsistencies
Wheel alignment drift
Drive motor faults or abnormal noises
Lost communication with cloud or on-prem fleet managers
We resolve these through sensor recalibration, part replacements, firmware upgrades, and network adjustments. Our team also verifies that your AMRs are safe and fully operational within your existing automation infrastructure.
Fleet-Wide Support for Multi-AMR Deployments
Running more than one AMR? We provide large-scale service support for facilities using fleet management software like MiR Fleet, FetchCore, or OTTO Fleet Manager.
From simultaneous diagnostics and synchronized software updates to calibration checks and performance balancing across units, our team ensures all your mobile robots operate efficiently as a system. We track service records per unit, monitor firmware compatibility, and help prevent small problems from cascading across your deployment. Our mobile robot troubleshooting services give you peace of mind—no matter how many robots you’re managing.
When to Schedule AMR Repair or Service
Watch for these signs your AMR needs inspection:
Slower navigation or path drift
Unresponsive safety sensors
Failing to dock or charge
Irregular battery behavior
Inaccurate mapping or lost routes
If you notice any of these issues, don’t delay. Early repair prevents system-wide delays, collisions, or hardware damage.
Request Your AMR Repair or Maintenance Service
Need help with AMR repair or want to build a proactive AMR maintenance plan? Our technicians are ready to inspect, repair, and support your mobile robot systems—onsite or remotely.
Reach out now to schedule service or talk with an expert about keeping your autonomous mobile robot fleet in peak condition.
We’ll get your system running smooth, safe, and ready for what’s next.
Talk A Robotics Integrator
By submitting this form, you agree to receive communications via phone, text message, and email. Message and data rates may apply. Your information may be shared with trusted third-party service providers solely for the purpose of helping you explore Section Robotic Intergration options. You also agree to our Privacy Policy and Terms of Service.
+1 463-257-9600
Success Stories: See What Business Have To Say About Robotics Integration
4.7 Customer Reviews
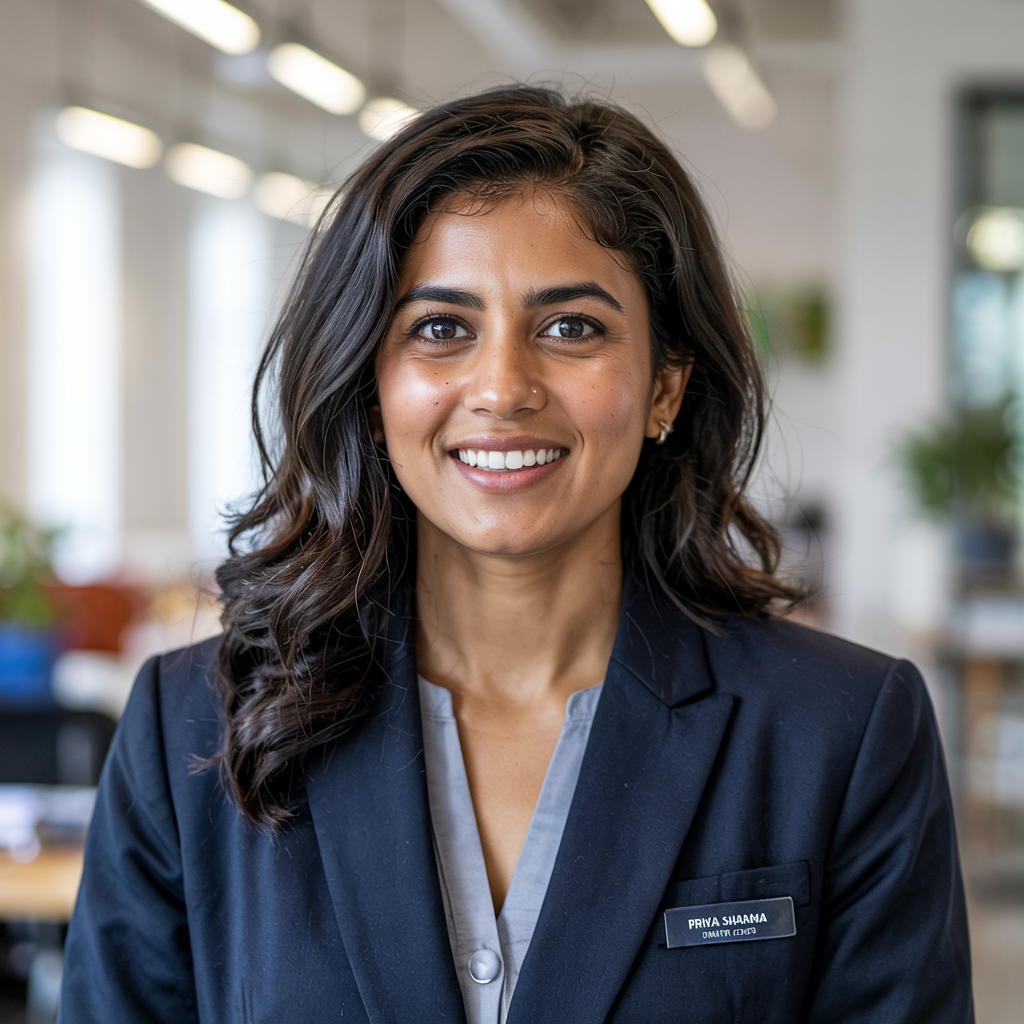
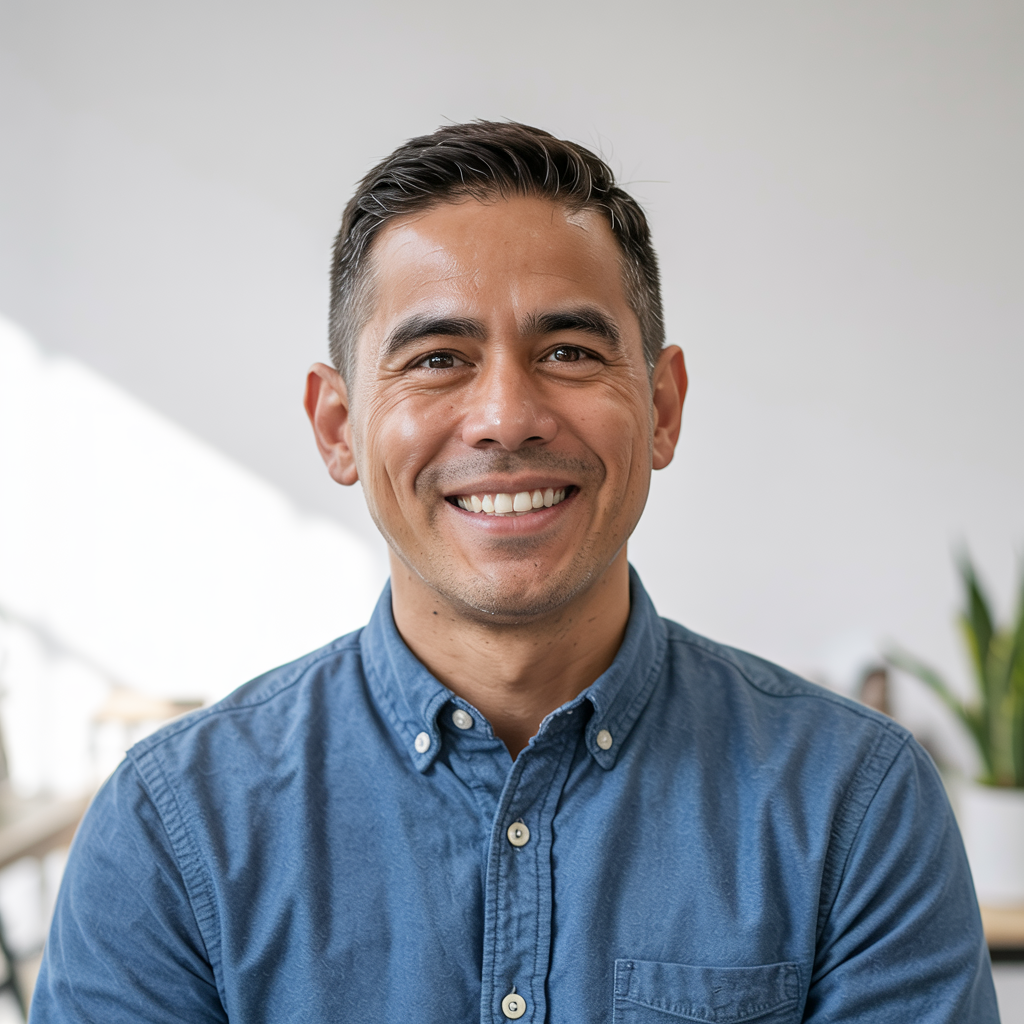
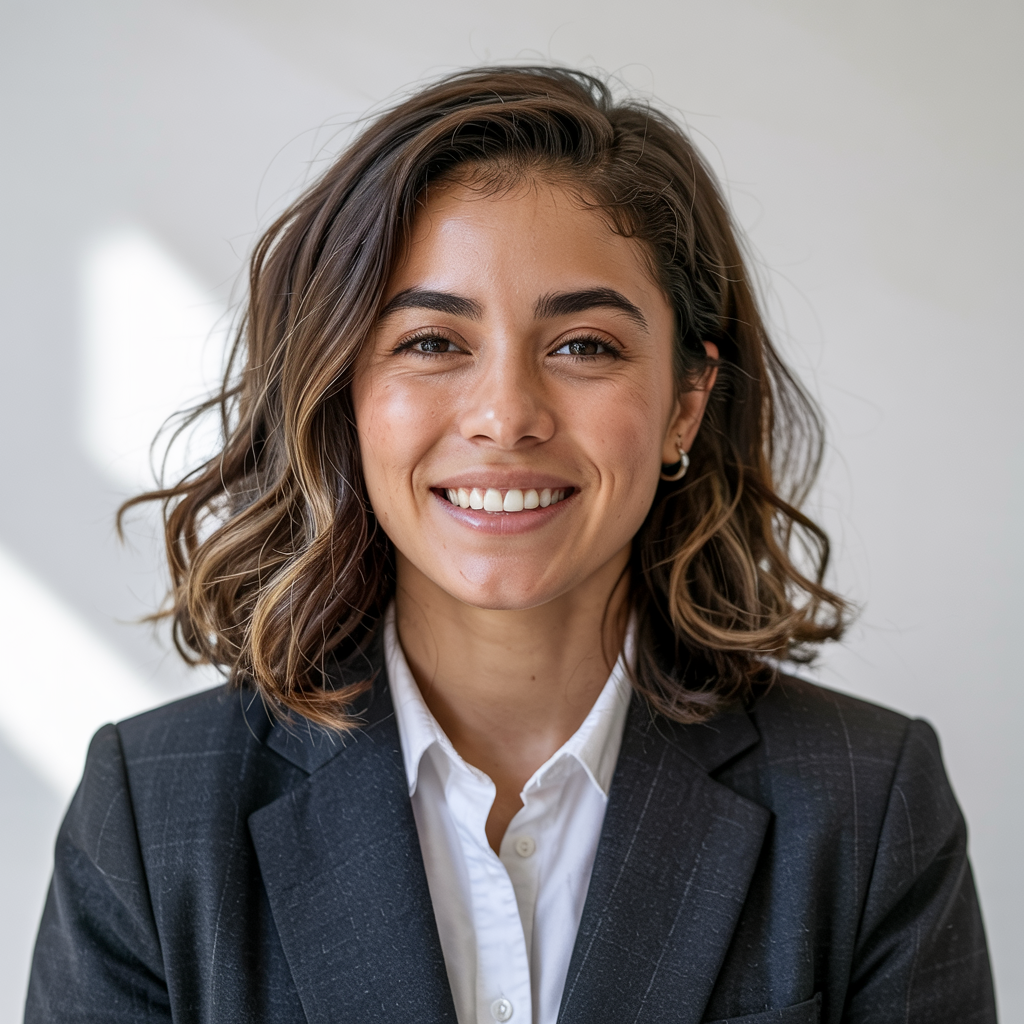